The Process Pillar: Achieving Operational Excellence Through Business Transformation
Table of Contents
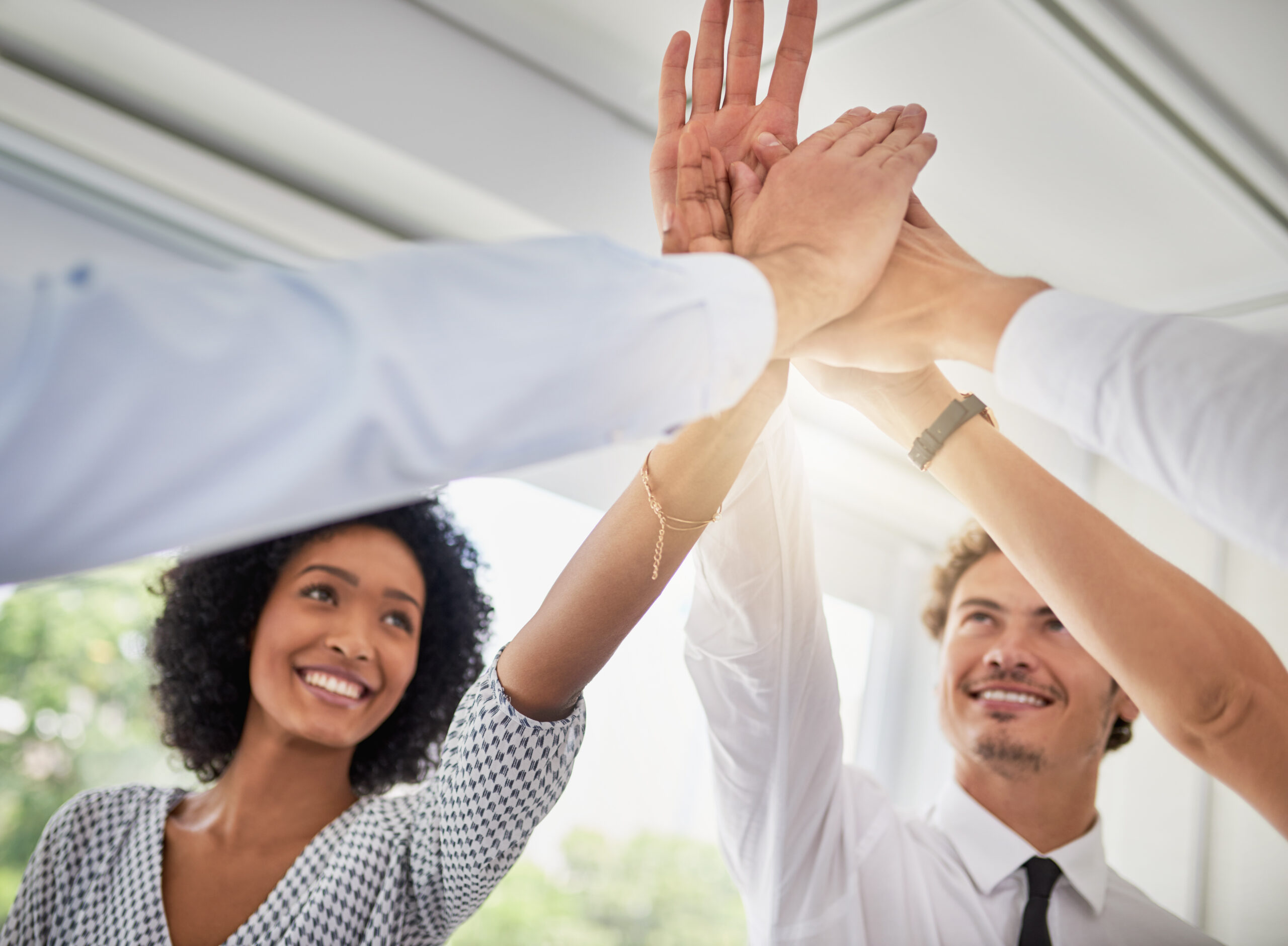
Executive Summary
Businesses are losing millions due to inefficient processes, yet many fail to address the root causes. With the economic climate impacting businesses of all sizes, operational excellence is no longer optional; it could really mean the difference between thriving or surviving. This white paper explores how leading organisations optimise processes using Lean management, Agile methodologies, and Continuous Improvement. Through research and targeted case studies, we provide actionable frameworks to eliminate inefficiencies, enhance adaptability, and measure success through proven metrics. We also acknowledge implementation challenges and technology enablers that influence outcomes.
Introduction: The Role of Process in Business Transformation
Business processes form the backbone of every organisation, yet inefficiencies often remain hidden. Research from the Lean Enterprise Institute (2023) reveals that 30% of work in an average company delivers no value to customers. Gartner (2023) estimates that organisations lose 20-30% of revenue to inefficient processes, while PwC (2022) reports that process breakdowns increase operational costs by 42%. Moreover, Forrester (2023) finds that organisations with poor process management score 37% lower on customer satisfaction.
Optimising processes is not just about cutting costs but enabling adaptability, scalability, and sustained market leadership. This paper outlines key methodologies for achieving operational excellence and transforming inefficiencies into competitive advantage, while providing realistic guidance on implementation challenges and timelines.
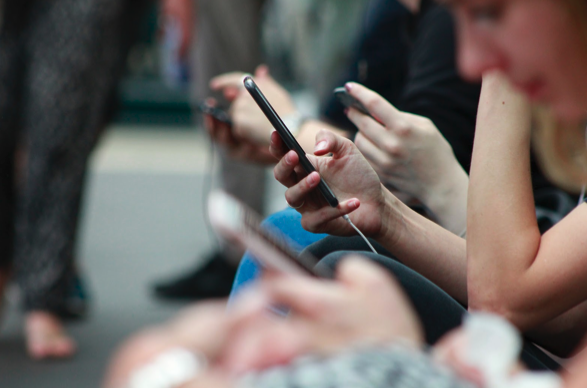
1. Achieving Operational Excellence Through Process Optimisation
Lean Management: Eliminating Waste, Enhancing Value
Lean thinking maximises customer value while minimising waste. Initially applied in manufacturing, Lean principles are now widely used across industries. The Lean Enterprise Institute reports that organisations adopting Lean experience a 25-30% reduction in operational costs, a 45-75% reduction in lead times, an 80% improvement in quality, and a 35-40% increase in productivity.
Agile Methodologies: Increasing Responsiveness and Adaptability
Initially developed for software, Agile methodologies have proven effective across industries by enabling iterative development, customer collaboration, and responsiveness to change. McKinsey research shows that Agile organisations are 2.7 times more likely to achieve top-quartile financial performance and bring products to market three times faster.
Continuous Improvement (Kaizen) vs. Six Sigma: Complementary Approaches
Many organisations struggle to determine when to apply Continuous Improvement (Kaizen) versus Six Sigma methodologies. While they share common goals, they serve different purposes and contexts:
Continuous Improvement (Kaizen) focuses on small, ongoing changes that deliver long-term gains. Deloitte research highlights that organisations with mature continuous improvement cultures achieve 3-5% higher productivity annually, a cumulative advantage over time. Kaizen works best for:
- Engaging frontline staff in improvement
- Addressing visible inefficiencies
- Creating cultural change around improvement
- Situations requiring minimal investment
Six Sigma applies a more structured, data-intensive approach to complex problems with significant variation. It’s most effective for:
- Processes with measurable defects
- Situations requiring root cause analysis
- Problems where the solution isn’t obvious
- High-value processes where small improvements yield significant returns
Successful organisations deploy both approaches strategically, using Kaizen for widespread engagement and Six Sigma for targeted, complex challenges.
Four key elements ensure successful continuous improvement implementation:
- Leadership commitment: Prioritising long-term improvement over quick fixes
- Employee engagement: Involving frontline staff who best understand processes
- Data-driven decision making: Using analytics rather than intuition
- Recognition and review: Reinforcing improvement through structured feedback
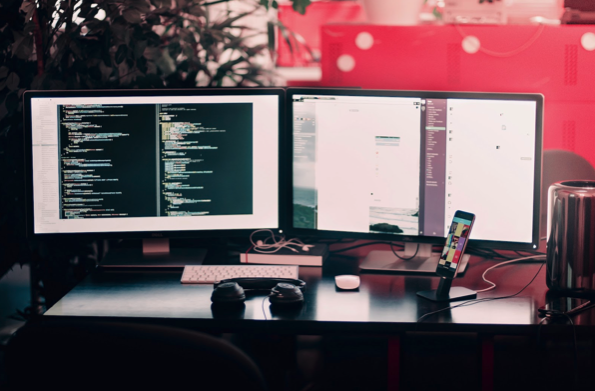
2. Proven Frameworks & Models for Process Improvement
Six Sigma & DMAIC: Data-Driven Excellence
Six Sigma reduces process variation and defects through structured problem-solving. The DMAIC framework (Define, Measure, Analyse, Improve, Control) underpins this approach:
- Define the problem and establish objectives
- Measure baseline data to identify inefficiencies
- Analyse root causes using statistical tools
- Improve the process by implementing targeted solutions
- Control changes to sustain long-term benefits
Business Process Reengineering (BPR): Fundamental Rethinking
In cases where incremental improvements are insufficient, Business Process Reengineering (BPR) enables radical redesign. Capgemini research shows that successful BPR initiatives reduce process times by 45-90% and decrease costs by 40-70%.
Value Stream Mapping (VSM): Visualising the End-to-End Process
Value Stream Mapping (VSM) helps organisations see inefficiencies that are otherwise difficult to detect. The Lean Management Journal reports that VSM typically identifies 20-40% of process steps that add no value. By mapping workflows, businesses can eliminate bottlenecks and reduce waiting times.
3. Technology Enablers for Process Excellence
Digital technologies are transforming how organisations approach process optimisation. Research by Forrester (2023) indicates that digitally enabled process improvements deliver 2.5 times greater impact than traditional approaches alone. Key technologies include:
Process Mining and Discovery
Process mining software analyses system logs to visualise how processes function, revealing deviations from expected workflows and identifying bottlenecks. According to Gartner, organisations using process mining reduce process analysis time by 80% and identify 25% more improvement opportunities compared to traditional methods.
Intelligent Automation
The automation spectrum has expanded beyond simple robotic process automation (RPA) to include:
- RPA: Rule-based automation for structured, repetitive tasks
- Intelligent Document Processing: AI-powered extraction and processing of unstructured data
- Conversational AI: Automated handling of customer and employee interactions
- Decision Automation: Algorithm-driven decision-making for complex scenarios.
IDC research shows organisations with mature automation strategies achieve 3-10x ROI on implementation costs.
Low-Code/No-Code Platforms
These platforms enable rapid process application development with minimal technical expertise. Forrester reports that low-code platforms accelerate application development by up to 10x, enabling business users to create and modify process applications without dependence on IT departments.
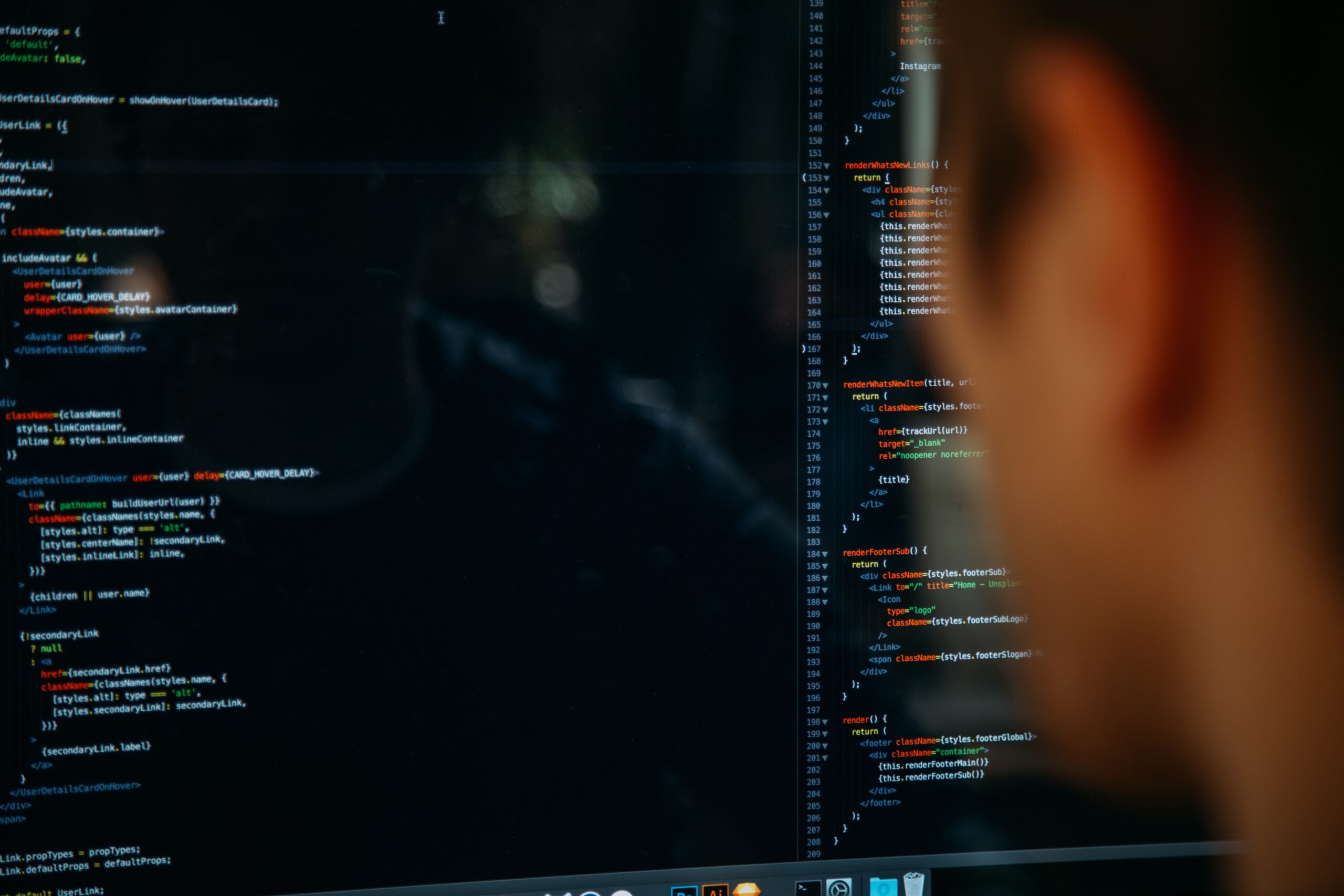
4. Measuring Success: Key Performance Indicators & Best Practices
Essential Process KPIs
High-performing organisations track four key process metrics:
- Cycle Time: Measures the time taken to complete a process
- First-Time-Right Percentage: Tracks error-free process completion
- Process Efficiency Ratio: Compares value-added time to total process time
- Cost Per Transaction: Evaluates the total cost of executing a process
According to research by the Process Excellence Network, industry leaders typically outperform competitors by 40-60% across these metrics.
Best Practices for Process Optimisation
Successful organisations employ:
- Data-driven decision making: Using analytics to optimise processes
- Cross-functional governance: Breaking down silos through shared process ownership
- Strategic automation: Reducing errors and speeding up execution
- Human-centred design: Ensuring user-friendly process redesigns
5. Comprehensive Case Study: Tesco's End-to-End Supply Chain Transformation
Between 2018 and 2022, Tesco implemented a comprehensive process transformation programme that effectively illustrates the integration of multiple methodologies. This case study demonstrates how a leading UK organisation successfully combined Lean, Agile and continuous improvement approaches within a complex operational environment.
Challenge
Tesco faced significant operational challenges despite its market leadership position:
- £1.2 billion in working capital tied up in excess inventory
- 3.5% waste in fresh food categories
- 87% product availability (below customer expectations)
- Rising fulfilment costs threatening online profitability.
Approach
Tesco’s transformation integrated multiple methodologies:
Lean Implementation
- Value stream mapping across the supply chain
- Standardised work procedures in warehouses
- Visual management systems for performance tracking
- Waste reduction in perishable goods handling.
Agile Store Operations
- Cross-functional store teams with end-to-end responsibility
- Daily huddles to address emerging issues
- Two-week improvement cycles
- Real-time adjustment to demand patterns.
Continuous Improvement Culture
- 12,000 staff trained in improvement techniques
- Idea capture and implementation system
- Recognition programme for successful improvements
- Regular Gemba walks by leadership.
Technology Enablement
- Predictive analytics for demand forecasting
- Process mining to identify bottlenecks
- Mobile apps for real-time inventory management
- Automated replenishment for stable product categories.
Implementation Challenges
Tesco encountered several significant obstacles during implementation:
- Technology adoption barriers: Initial analytics tools were too complex for store teams to use effectively. Tesco addressed this by implementing a “tech buddy” system pairing analytics experts with store teams and simplifying dashboards to focus on actionable metrics.
- Change fatigue: After initial enthusiasm, improvement momentum slowed during year two. The company responded by celebrating early wins, adjusting the pace of change, and enhancing communication around benefits realisation.
- Process fragmentation: Initial improvements created local optimisation at the expense of end-to-end performance. Tesco resolved this by establishing cross-functional process ownership and implementing integrated performance metrics.
Results
The transformation delivered substantial benefits across multiple dimensions:
- £380 million reduction in inventory costs
- 45% decrease in fresh food waste
- Product availability improved to 96%
- 30% reduction in online fulfilment costs
- 18% improvement in customer satisfaction.
Importantly, the full transformation took 4 years to complete, with benefits accelerating in years 3-4 as improvements reinforced each other and cultural changes took root. This timeline underscores the need for sustained commitment when undertaking comprehensive process transformation.

6. Implementation Framework: A Realistic Approach
Assessment and Prioritisation
A structured Process Maturity Assessment identifies gaps in process design, execution, and governance. According to Gartner, organisations that conduct thorough assessments are 2.3 times more likely to succeed in transformation.
Common assessment pitfalls include:
- Over-reliance on documented processes instead of actual practices
- Failure to include frontline perspective
- Not considering customer impact of internal processes
- Inadequate benchmarking against industry standards.
Implementation Roadmap: Realistic Timelines
A phased approach ensures sustainable change, with timeframes varying based on organisational size and complexity:
1. Foundation Building (3-6 months)
- Process maturity assessment
- Opportunity prioritisation
- Capability gap analysis
- Initial skill development
- Quick win implementation (2-3 high-impact projects)
2. Capability Development (6-12 months)
- Methodology training (Lean, Agile, Six Sigma)
- Governance structure implementation
- Process ownership clarification
- Measurement system deployment
- Technology enablement planning
2. Systemic Transformation (12-24 months)
- Cross-functional process redesign
- Technology implementation
- Work standardisation
- Management system alignment
- Change management and communication
4. Continuous Evolution (Ongoing)
- Innovation pipeline development
- Knowledge sharing mechanisms
- Performance tracking and refinement
- Recognition and reward systems
- External benchmarking and renewal.
Common Implementation Challenges and Mitigation Strategies
McKinsey research shows that 70% of process transformation initiatives fail to meet all objectives. Common challenges include:
- Change Resistance: Traditional stakeholders often resist new methodologies. To mitigate this, key influencers should be involving early, early wins should be demonstrated, and robust training should be provided.
- Capability Gaps: Many organisations lack expertise in process methodologies. Effective approaches include developing internal champions, targeted external hiring, and phased capability building.
- Technology Integration: Legacy systems often impede process improvements. Successful organisations implement process changes parallel to technology modernisation, using APIs and middleware to bridge gaps.
- Sustainability Challenges: Initial improvements often erode without proper systems. To maintain gains, leading organisations establish robust governance, regular reviews, and aligned incentives.
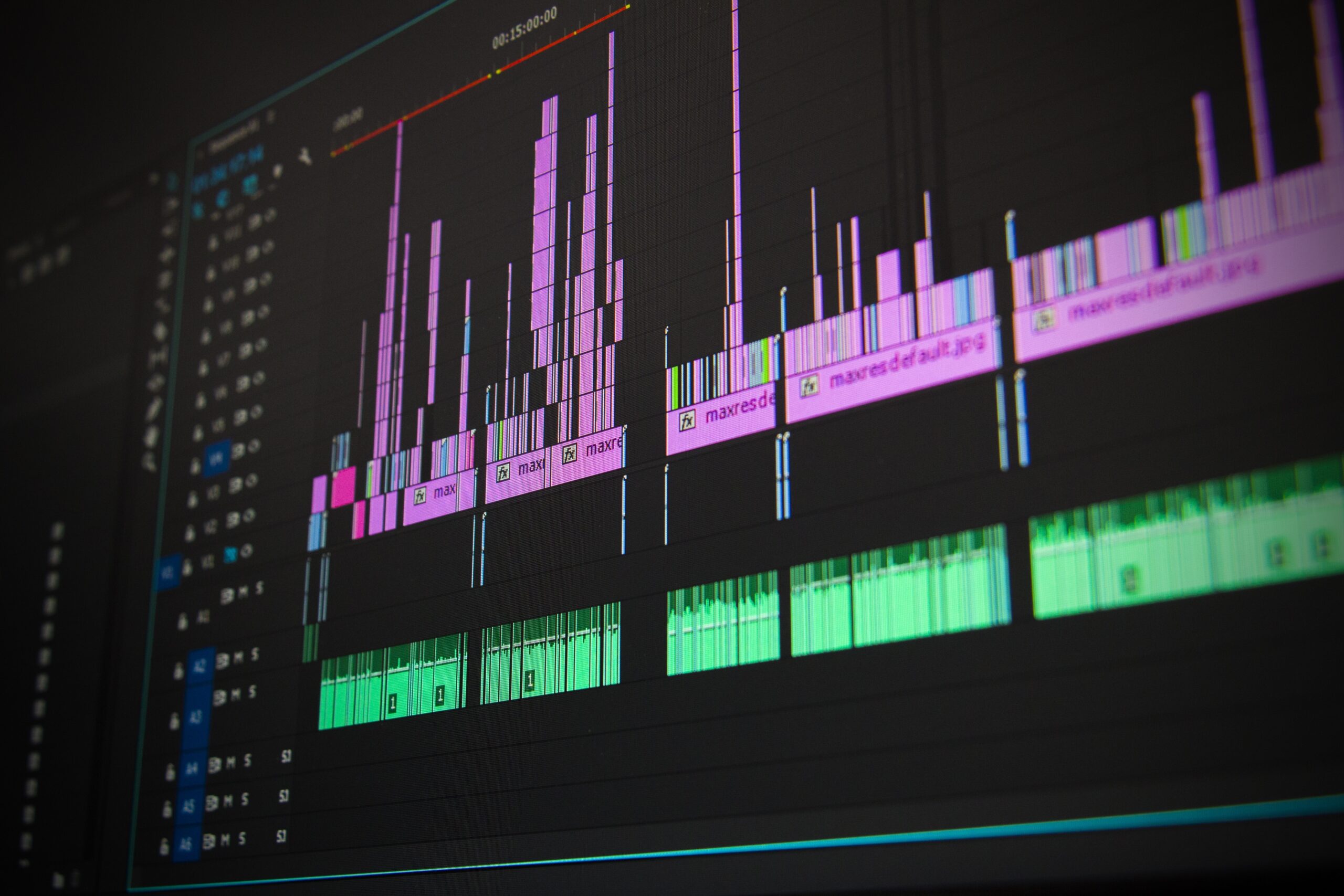
Conclusion: The Competitive Advantage of Process Excellence
Optimising processes enables businesses to be more responsive, efficient, and adaptable. Companies with top-quartile process performance achieve 3-5 times higher profitability growth (MIT Sloan, McKinsey). Process excellence frees leadership to focus on strategy while ensuring long-term operational resilience.
In today’s volatile business environment, the ability to adapt processes quickly provides a crucial competitive advantage. Organisations that excel at process management demonstrate greater resilience during disruption and faster recovery from setbacks.
Your Next Steps with Tratech Consulting
Tratech Consulting brings proven methodologies to help you achieve process excellence:
- Process Maturity Assessment: Evaluate your current capabilities against industry benchmarks and identify high-value improvement opportunities
- Process Optimisation Workshop: Engage key stakeholders to prioritise initiatives and develop a tailored implementation roadmap
- Transformation Support: Access expertise and tools to accelerate your journey to process excellence.
Contact details
- Book a call
- 01252 929319
- info@tratechconsulting.co.uk
- Abbey House, 282 Farnborough Road, Farnborough, Hampshire, GU14 7NA
-
Monday to Friday
9:00am - 5:30pm